1. Introduction
The blast furnace, a towering giant in the ironmaking industry, has witnessed significant technological advancements over the years. One of the most impactful innovations is Pulverized Coal Injection (PCI), which has transformed the efficiency and sustainability of iron production (Figure 1). In this blog, we delve into the intricacies of PCI, its benefits, and the technical marvel behind its implementation in the blast furnace raceway.
PCI involves grinding coal into a fine powder and injecting it directly into the blast furnace’s raceway via specialized lances. This process serves as a substitute for a portion of the coke traditionally used in the furnace, providing several economic and environmental advantages.
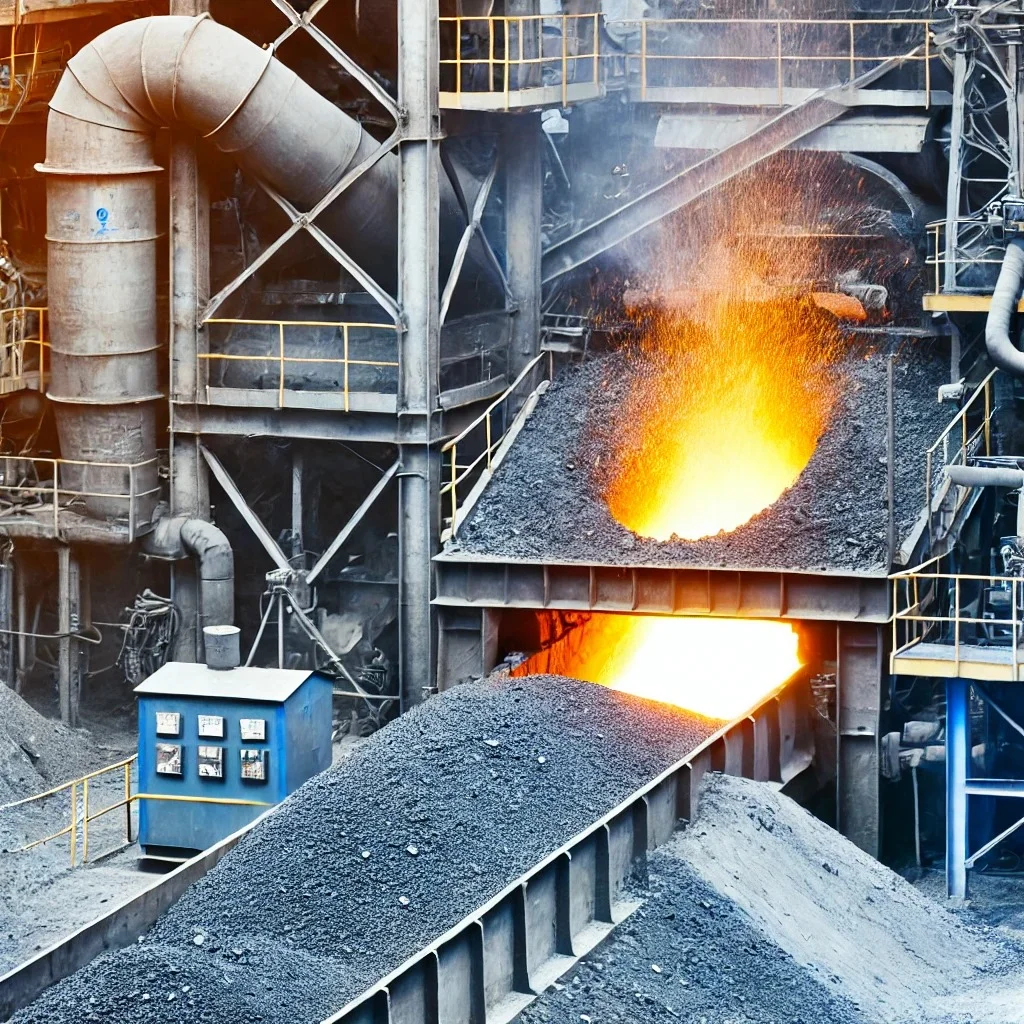

Figure 1. Schematic of the lower zone of the blast furnace.
2. Key Components of PCI
Pulverized Coal Preparation: Coal is finely ground to enhance its combustion efficiency. The particle size is typically less than 75 μm, ensuring a quick and complete combustion.
Storage and Handling: The pulverized coal is stored in bins or silos and transported pneumatically to the blast furnace injection points.
Injection System: Specially designed lances ensure the precise delivery of pulverized coal into the furnace, mixing effectively with the hot blast air.
3. The Combustion Process in the Raceway
The raceway is a high-temperature zone in front of the tuyeres, where the hot blast air is introduced into the furnace. Here, the injected pulverized coal undergoes rapid combustion, releasing heat and generating essential reducing gases such as carbon monoxide (CO) and hydrogen (H2). These gases play a crucial role in reducing iron ore into molten iron.
3.1. Key Chemical Reactions
- Combustion: C + O2 → CO2
- Boudouard Reaction: C + CO2 → 2CO
- Water-Gas Reaction: C + H2O → CO + H2
These reactions provide the necessary thermal energy and reducing agents, facilitating efficient iron production.
4. Advantages of PCI in Blast Furnaces
Reduced Coke Consumption: Coke is an expensive and carbon-intensive material. By injecting pulverized coal, which is cheaper, the furnace’s reliance on coke is significantly reduced, leading to cost savings and lower CO₂ emissions from coke production.
Cost Efficiency: Pulverized coal is generally more economical than coke. The reduction in coke consumption directly translates into reduced production costs, making the process more financially viable.
Environmental Benefits: Decreasing coke usage also means fewer emissions of pollutants such as NOx and SOx, making PCI a cleaner alternative. Additionally, the overall CO₂ footprint of ironmaking is lowered, contributing to a more sustainable operation.
Improved Furnace Efficiency: The heat generated from coal combustion enhances the thermal efficiency of the furnace. This improvement leads to better control over furnace temperatures and more efficient reduction reactions.
5. Challenges and Considerations
While PCI offers numerous benefits, its successful implementation requires careful consideration of several factors:
Injection Consistency: Ensuring a steady and uniform flow of pulverized coal is crucial to avoid combustion inefficiencies and temperature fluctuations within the furnace.
Coal Quality: The quality of the coal, including its ash content and volatility, can impact the combustion process and the quality of slag produced. Proper selection and blending of coal types are essential for optimal performance.
Operational Adjustments: The introduction of PCI necessitates adjustments in furnace operation, such as tweaking blast temperature and oxygen levels. Operators must closely monitor and control these parameters to maintain stable operations.
Slag Management: The ash from the injected coal contributes to the slag burden. Effective slag management is necessary to prevent operational issues and ensure smooth furnace performance.
6. The Future of PCI in Ironmaking
As environmental regulations become more stringent and the industry continues to seek cost-effective and sustainable solutions, PCI technology is poised for further advancements. Modern control systems and real-time monitoring are enhancing the precision and efficiency of PCI operations, while ongoing research into alternative coal blends and injection techniques promises even greater improvements.
In conclusion, PCI in blast furnace raceways represents a significant leap forward in ironmaking technology. By reducing reliance on coke, cutting costs, and minimizing environmental impact, PCI is revolutionizing the industry and paving the way for a more sustainable future. As we continue to innovate and refine this technology, the potential for even greater efficiency and environmental benefits will undoubtedly grow, ensuring that the blast furnace remains a cornerstone of iron production for years to come.