Imagine hurtling through the air at several times the speed of sound. That’s the realm of hypersonic vehicles, the future of ultra-fast travel. Designing these marvels comes with significant challenges in the form of immense pressure and heat loads. One critical tool in this field is Fluid-Structure Interaction (FSI), which provides a comprehensive understanding of how fluids (like air) interact with solid structures (such as aircraft wings and fuselages). In this blog, we will explore the principles of FSI, its importance in high-speed vehicles, and its practical applications in aerospace design.
Understanding Fluid-Structure Interaction (FSI)
Fluid-Structure Interaction (FSI) involves the interplay between fluid dynamics and structural mechanics. Traditional engineers analyze a vehicle’s structure and the surrounding airflow separately. But at hypersonic speeds, things get complicated. The air flowing around the vehicle (the fluid) exerts tremendous forces, not just pushing against it but also heating it up due to shockwaves. This heat, in turn, affects how the vehicle’s structure (think wings, fuselage, missile fins) behaves. Traditional methods wouldn’t capture this crucial two-way interaction.
FSI bridges this gap by treating the airflow and the structure as a coupled system. It essentially asks: “How does the structure respond to the airflow, and how does that response affect the airflow itself?” By considering this feedback loop, FSI provides a much more accurate picture of what’s happening to the vehicle. One approach to analyze and understand fluid-structure interaction is through experiments and flight tests, although these techniques are very expensive, especially at high speeds. Alternatively, Computational Fluid Dynamics (CFD) can be used to analyze fluid flow, and Finite Element Analysis (FEA) can be used to study structural responses. However, FSI integrates these analyses to reflect real-world scenarios where fluid flow can deform structures, and those deformations can, in turn, alter the fluid flow.
Benefits of Using FSI for Hypersonic Vehicles
High-speed vehicles, such as supersonic missiles and hypersonic spacecraft, operate under extreme conditions that make FSI particularly valuable:
- Aerodynamic Forces: At high speeds, vehicles encounter significant aerodynamic pressures that can deform structural components. FSI helps predict these deformations and their effects on overall vehicle performance.
- Thermal Loads: High-speed flight generates substantial heat, especially at the leading edges and nose of the vehicle. This heat can alter material properties, affecting stiffness and potentially leading to failure. Shockwaves can significantly increase the pressure and heat loads on the structure. FSI models these thermal effects, enabling better material selection and design.
- Non-Linear Phenomena: The unsteady nature of turbulence can create vibrations and stresses in the structure. The complex nature of high-speed flows can induce non-linear behaviors like flutter—an instability caused by the interaction between aerodynamic forces and structural vibrations. FSI allows for early detection and mitigation of such phenomena, preventing potential structural failures.
- Dynamic Interactions: The interaction between aerodynamic forces, structural responses, and thermal loads can lead to dynamic changes that are difficult to predict using traditional methods. FSI provides a more accurate and integrated approach to these challenges.
Boosting Accuracy
FSI simulations can predict the complex interplay between the airflow and the structure, leading to more realistic predictions of the vehicle’s behavior. This allows engineers to identify potential problems before they even build the first prototype.
Preventing Disasters
FSI helps pinpoint weaknesses in the structure that could lead to catastrophic failures like flutter (rapid oscillations) or buckling (sudden deformation). By identifying these risks early on, engineers can take steps to strengthen the structure or adjust the design.
Optimizing Designs
FSI allows engineers to see how even minor changes in the structure can affect the airflow. This knowledge can be used to create lighter, more aerodynamic vehicles that require less fuel to reach hypersonic speeds.
Applications of FSI in Aerospace Engineering
FSI is instrumental in the design and analysis of various aerospace components:
- Inlets and Nozzles: These internal structures manage airflow into and out of engines. FSI helps optimize their design for efficient performance under high-speed conditions.
- Fins, Wings, and Control Surfaces: External structures face significant aerodynamic forces. FSI aids in designing these components to endure these forces while maintaining optimal performance. An FSI study of a missile fin carried out shows the results from CFD and FEA one-way simulations. These figures indicated the flow features obtained from the fluid flow simulations and associated deformations.
- Thermal Structural Analysis: Predicting how thermal loads will affect structural integrity is crucial. FSI provides insights into material behavior under high temperatures, helping engineers choose suitable materials and designs.
- Flutter Analysis: By studying the interaction between aerodynamic forces and structural vibrations, FSI helps prevent flutter-related issues, ensuring the safety and stability of high-speed vehicles.
Challenges and Future Directions
Despite its advantages, applying FSI to high-speed vehicles presents challenges. Accurately recreating the thermal and aerodynamic conditions experienced during flight is difficult, and wind tunnel experiments often fall short due to scaling issues. Computational models, while powerful, require significant resources to simulate complex interactions. However, advancements in computational power and modeling techniques are continually improving the accuracy and efficiency of FSI analyses.
Learning from the Past, Shaping the Future
Past hypersonic vehicles like the X-15 offer real-world examples of why FSI is crucial. The X-15 experienced issues like melting near shockwaves and fatigue cracks likely caused by flutter. These events highlight the need for a more comprehensive design approach that considers FSI. As hypersonic technology continues to develop, FSI will be at the forefront, ensuring the safety and efficiency of these incredible vehicles. By combining advanced computer simulations with wind tunnel experiments, engineers can gain a deeper understanding of FSI and pave the way for the next generation of hypersonic flight. So, the next time you hear about a hypersonic vehicle soaring through the sky, remember the silent hero behind it all: fluid-structure interaction, keeping the vehicle in one piece while it breaks the sound barrier and beyond.
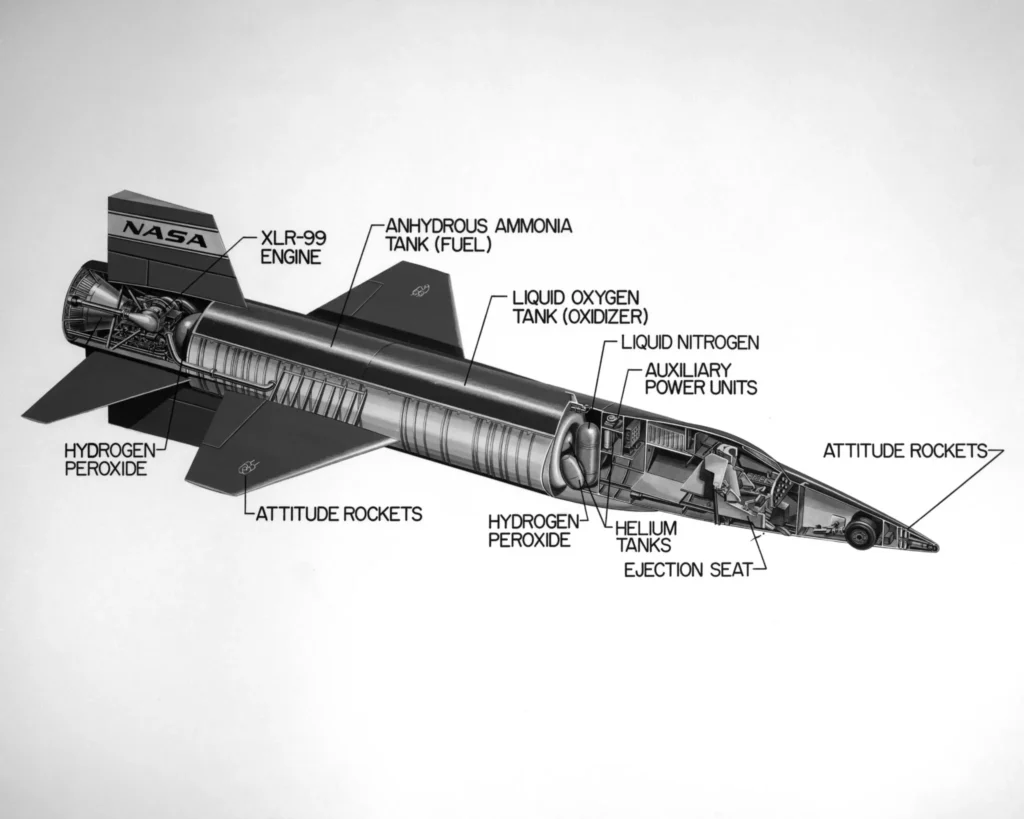
Figure refer : https://www.nasa.gov/reference/x-15/
Historical and contemporary examples highlight the importance of FSI in aerospace engineering. The X-15 rocket plane experienced thermal buckling and flutter-related damage due to intense heating near shock waves. In contrast, the SR-71 Blackbird benefited from extensive thermomechanical testing, showcasing the value of thorough FSI analysis. Ongoing research initiatives, such as those funded by the German Research Foundation, continue to push the boundaries of our understanding, leading to more reliable and efficient high-speed vehicle designs.
Conclusion
Fluid-Structure Interaction (FSI) is a critical framework for understanding and optimizing the performance of high-speed vehicles. By integrating fluid dynamics and structural mechanics, FSI provides a comprehensive approach to predicting and mitigating the complex interactions that occur in high-speed flight. As technology advances, the role of FSI in aerospace engineering will only grow, paving the way for innovative solutions to the challenges of high-speed flight and ensuring the safety and efficiency of future aerospace vehicles.